10 Best Cement Companies in India You Should Know
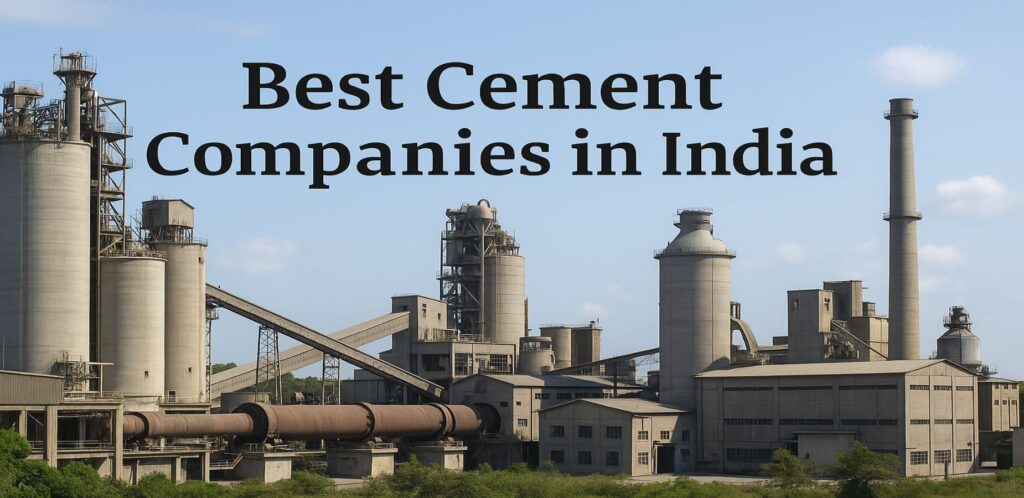
India is the world’s second-largest cement producer, with an installed capacity of more than 600 million tonnes per year. The Indian cement industry is key to the nation’s infrastructure, fueling everything from high roads and bridges to residential and commercial construction. With consistent growth led by urbanization, industrialization, and infrastructure development projects supported by the government, the industry is expected to hit USD 50 billion by 2030, based on industry estimates.
Cement is not a binding material—it is the backbone of modern construction. From mega rail networks to rural housing projects, there is a perpetual and growing need for high-quality, long-lasting cement. It makes the cement industry not only indispensable but also competitive.
In this blog, we highlight the Top 10 Cement Companies in India that are making waves in their production capacity, market share, innovation, and sustainability efforts. As a builder, investor, or even an inquisitive observer of India’s industrial prowess, this list provides important insights into the companies literally building the foundation for India’s future.
Overview on the Cement Industry in India
India’s cement industry is the pillar of the country’s infrastructure and economic growth. Driven by strong demand factors and strong production capacities, the industry has every prospect to grow steadily in the future.
Second-largest producer in the world
India is the second-largest cement-producing country in the world, accounting for more than 8% of global cement output. The abundant limestone deposits, increasing construction industry, and robust manufacturing sector of the country have allowed it to hold this leadership role for decades.
Production capacity: More than 600+ million tonnes annually (as of 2024)
As of 2024, India has an installed cement manufacturing capacity of over 600 million tonnes per annum (MTPA). This capacity is spread across over 200 large and mini cement plants, with private sector players ruling the roost. Large players are upgrading facilities continuously and adding capacity to cater to growing domestic and export demand.
- Key growth drivers:
- Urbanization: India is likely to have almost 600 million urban residents by 2036, resulting in gigantic construction activity.
- Infrastructure push: Government-sponsored projects such as highways, metros, and smart cities have driven an all-time high consumption of cement.
- Real estate boom: Fast growth in commercial and residential construction—particularly in Tier II and III cities—has generated consistent demand.
- Rural housing and industry growth: Demand for cement also increases through rural housing plans and the establishment of industrial parks and logistics centers.
Major production regions/states
The most significant cement-producing states in India are:
- Andhra Pradesh and Telangana: rich in limestone belts and possessing large integrated cement factories.
- Rajasthan: characterized by vast reserves and acting as a central supply hub for North India.
- Chhattisgarh: provides access to coal and limestone, fueling some huge factories.
- Gujarat and Tamil Nadu: make a major contribution with coastal plants and export facilities.
These states are well-served by the availability of natural resources, industrial infrastructure, and road and rail networks.
Government efforts driving the sector
- Smart Cities Mission: Plans 100 smart cities, fueling mass-scale urban development.
- PM Awas Yojana (PMAY): Aims to provide affordable housing for all by 2025, fuelling huge demand for rural and urban housing.
- Bharatmala Project: A road development initiative that is improving connectivity within India and driving the consumption of cement.
- Sagarmala Project: Port infrastructure and logistics-based, it is generating demand for high-grade cement for coastal and industrial projects.
These schemes collectively generate steady and long-term demand for cement across sectors.
India’s cement sector, based on high demand and strategic growth, is set to continue as a major force in international markets while also serving to drive the nation’s aggressive infrastructure plans.
List of Top 10 Cement Companies in India
1. UltraTech Cement Limited
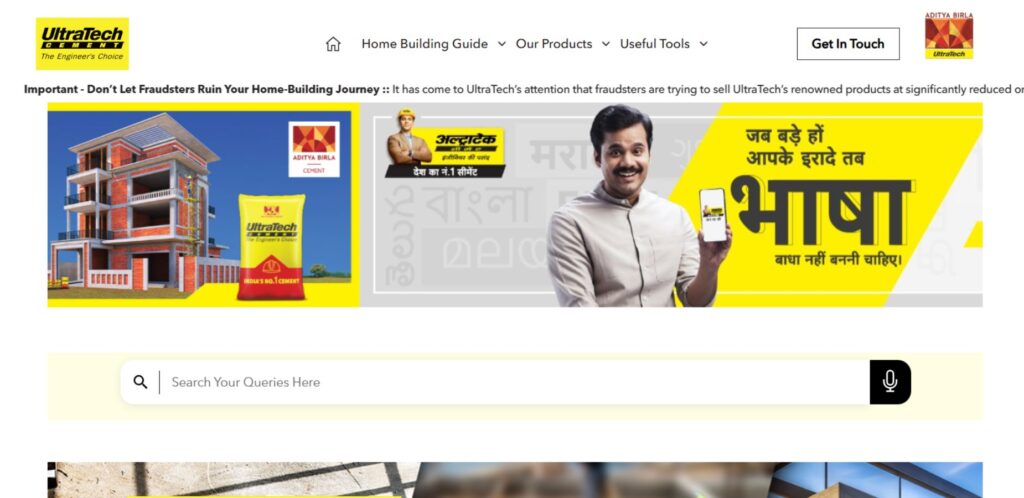
UltraTech Cement Limited, a subsidiary of the Aditya Birla Group, is India’s largest grey cement, white cement, and ready-mix concrete manufacturer and one of the leading cement producers in the world.
Its headquarters is in Mumbai and is renowned for having a strong operational presence, state-of-the-art manufacturing techniques, and relentless emphasis on innovation and sustainability.
The firm is an integral part of the infrastructure development of India by serving across a vast spectrum of industries such as housing, commercial, and industrial building.
Production Capacity:
- Total installed grey cement capacity: 152.7 million tonnes per annum (MTPA)
- White cement capacity (through Birla White): 1.5 MTPA
- Ready Mix Concrete (RMC) plants: Over 240+ units across India
- Targeted capacity: 200+ MTPA by FY27
Key Plants/Locations:
- Integrated plants: 23 across states like Rajasthan, Chhattisgarh, Andhra Pradesh, Tamil Nadu, and Gujarat
- Clinkerisation unit: Located in the UAE
- Grinding units: 26, including those in Maharashtra, West Bengal, Bihar, Odisha, and Uttar Pradesh
- Bulk terminals: 7 strategically located along the Indian coastline for bulk cement movement
- Key project expansions: Dhule (Maharashtra), Dalla (UP), Jharsuguda (Odisha), Cuttack (Odisha)
Sustainability Initiatives:
- Green energy use: 691 MW of green energy (262 MW from WHRS and 429 MW from renewable sources)
- Water stewardship: Achieved 5x water positivity, saving over 105 million m³ in FY24
- Carbon reduction: Partnered with CarbonOrO, Coomtech, and Fortera for carbon capture and utilization
- First to trial Coolbrook’s RotoDynamic Heater in India to eliminate fossil fuels in production
- Plastic negative: Uses more plastic waste than it generates by co-processing in cement kilns
- GreenPro-certified products: Over 70 cement products certified for eco-friendliness
- Circular economy: Practices like zero-discharge RMC plants, fly ash reuse, and municipal waste processing
Website: www.ultratechcement.com
2. Birla Corporation Limited
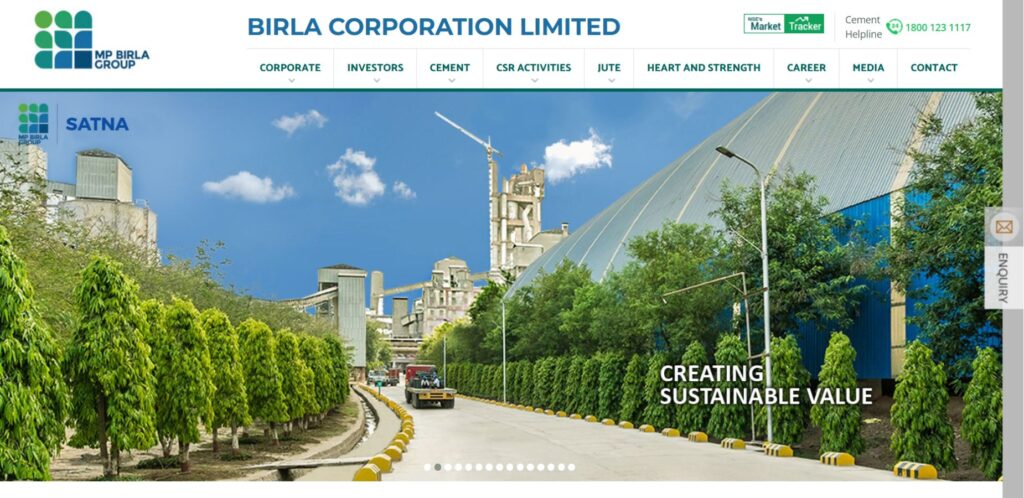
Birla Corporation Limited, the M.P. Birla Group’s flagship company, is a name well-respected and tried over time in India’s cement industry. Established more than a century ago, the company has matured as a vibrant entity within the cement industry, reputed for its quality, operating excellence, and local presence.
Year by year, Birla Corporation has been able to spread its presence from central, eastern, and northern India, bringing together the latest in technology with strong commitment to sustainable development. While pursuing challenging capacity expansion, the company continues to keep performance and environmental responsibility in balance.
Production Capacity:
- Current installed capacity: Approximately 20 million tonnes per annum (MTPA)
- Major expansion: Mukutban greenfield plant (Maharashtra) added 3.9 MTPA in 2022
- Upcoming growth: Plans to reach 25 MTPA by FY 2025–26 through new clinker and grinding units
- Long-term vision: Scale operations to 30 MTPA by 2030
Key Plants/Locations:
- Madhya Pradesh: Satna, Maihar (integrated plants)
- Maharashtra: Mukutban (integrated), Butibori (grinding unit)
- Uttar Pradesh: Raebareli, Kundanganj (grinding units)
- Rajasthan: Chanderia
- West Bengal: Durgapur
- Total of 10 manufacturing units across 8 strategic locations in India
Sustainability Initiatives:
- Green Energy Adoption:
- 41.2 MW of solar power installed across key plants
- 43.35 MW Waste Heat Recovery Systems (WHRS) to reduce thermal energy use
- Alternative Fuels & Raw Materials (AFR):
- Over 1.2 lakh tonnes of industrial and agricultural waste used as fuel in FY23
- Clinker Factor Reduction:
- Promotes use of fly ash, slag, and other supplementary materials to lower carbon intensity
- Circular Economy Practices:
- Focus on energy efficiency, resource reuse, and minimization of environmental footprint
Website: www.birlacorporation.com
3. Ambuja Cements Limited
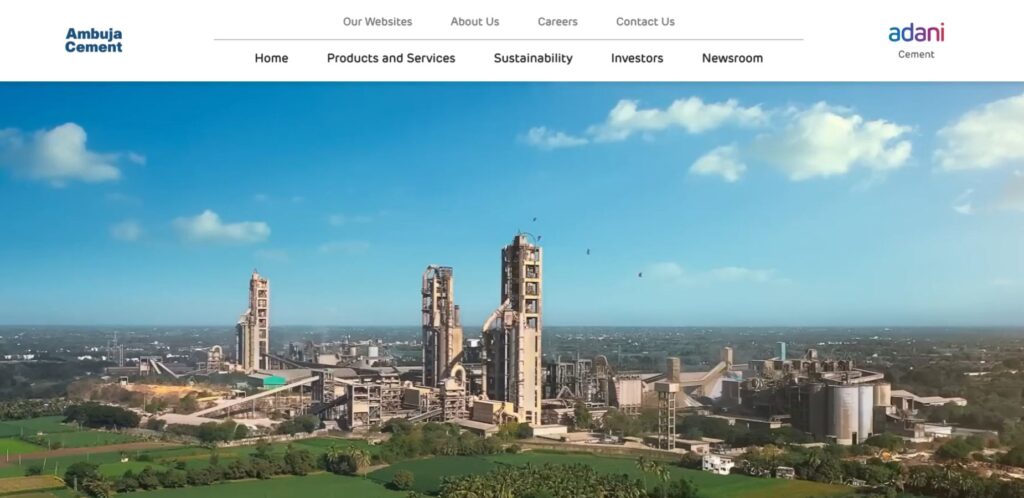
Ambuja Cements Limited, which is part of the Adani Group, is one of India’s premier cement producers with a rich tradition of innovation, efficiency, and sustainability. Established in 1983, the company has always been dedicated to producing high-performance cement solutions while adhering firmly to sound manufacturing practices.
With an aggressively growing capacity for production and a broad national footprint, Ambuja is well-placed to help meet India’s ambitious infrastructure and housing ambitions. It is particularly renowned for its operational excellence and green manufacturing leadership within the Indian cement industry.
Production Capacity:
- Current installed capacity: Approximately 100 million tonnes per annum (MTPA)
- Targeted growth: Planned expansion to 118 MTPA by FY 2026 and 140 MTPA by FY 2028
- Operational footprint: Includes 18 integrated plants and 14 grinding units, including recent acquisitions such as Sanghi Cement and Penna Cement
Key Plants/Locations:
- Integrated manufacturing units: Located in key states such as Gujarat, Maharashtra, Rajasthan, Punjab, Himachal Pradesh, Chhattisgarh, and West Bengal
- Grinding units: Spread across Bihar, Tamil Nadu, Odisha, and other states, enhancing regional coverage
- Recent expansion: A new 6 MTPA grinding unit announced in Bihar as part of continued capacity growth
Sustainability Initiatives:
- Green energy leadership:
- Operating 189 MW of green power, with plans to scale up to 1,000 MW by FY 2026
- Targeting 60% of total power to come from renewable sources by FY 2028
- Waste Heat Recovery Systems (WHRS):
- Current capacity at 103 MW, set to reach 397 MW to improve energy efficiency
- Alternative Fuels and Raw Materials (AFR):
- Increasing thermal substitution rate (TSR), targeting 27% by 2030
- Focus on co-processing industrial and municipal waste in kilns
- Environmental achievements:
- 11x water positive status with zero wastewater discharge
- 8x plastic negative, recycling more plastic waste than consumed
- Several units certified as “Zero Waste to Landfill” facilities
- Long-term vision:
- Committed to net-zero carbon emissions by 2050
- Actively pursuing afforestation, ESG compliance, and carbon-reduction technologies
Website: www.ambujacement.com
4. India Cements Limited
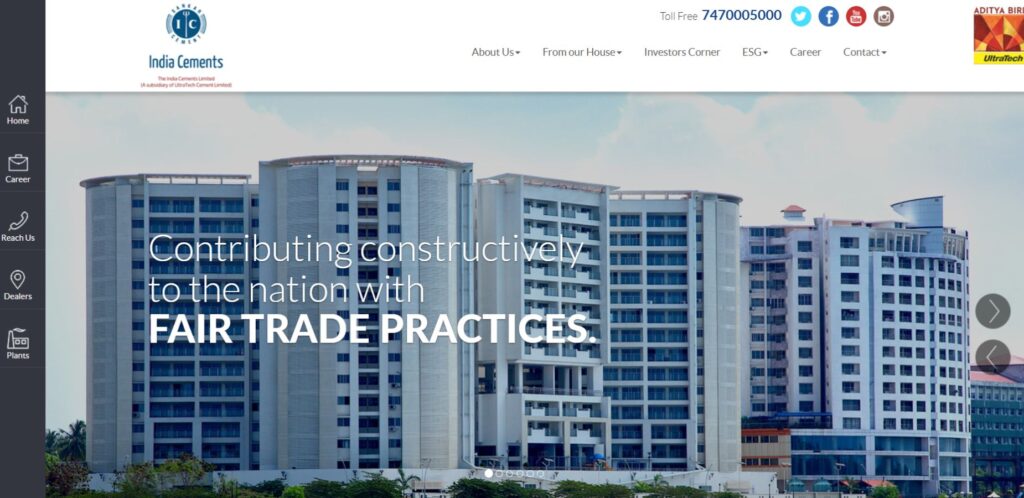
India Cements Limited, established in 1946 and headquartered in Chennai, is a leading southern Indian cement producer that is now part of the UltraTech Cement group as of December 2024.
With a solid geographic presence and well-regarded brands such as Sankar Cement, Coramandel Cement, and Raasi Gold, the company backs residential and infrastructure construction endeavors. Riding a century-old heritage, India Cements builds on its operations by expanding abroad, embracing sustainable techniques, and engaging with communities.
Production Capacity:
- Installed capacity: Approximately 14.75 million tonnes per annum (MTPA) up from 14.45 MTPA following recent upgrades
- Facility breakdown:
- 8 integrated cement plants across Tamil Nadu, Telangana, Andhra Pradesh, and Rajasthan
- 2 grinding units one each in Tamil Nadu and Maharashtra
- Expansion efforts: Incremental capacity increases, such as at the Banswara plant, indicate steady growth
Key Plants/Locations:
- Tamil Nadu: Multiple integrated plants, including the historic Sankarnagar (Thalaiyuthu) facility
- Telangana & Andhra Pradesh: Integrated units serving southern markets
- Rajasthan: Integrated facility via subsidiary Trinetra Cement
- Grinding units: Located in Tamil Nadu and Maharashtra to optimize regional supply
Sustainability Initiatives:
- Environmental focus: Emphasis on reducing emissions, promoting energy efficiency, and developing green belts around plant areas
- Water conservation: Extensive use of rainwater harvesting, recycling systems, and water reuse practices across facilities
- Renewable energy use: Adoption of solar power and waste heat recovery systems, along with co-processing of waste materials
- Circular economy: Commitment to waste-to-energy, reuse of by-products, and efforts to reduce landfill contributions
- CSR and community engagement: Focused programs in education, healthcare, sanitation, and rural infrastructure, especially in plant-adjacent areas
Website: indiacements.co.in
5. Shree Cement Limited
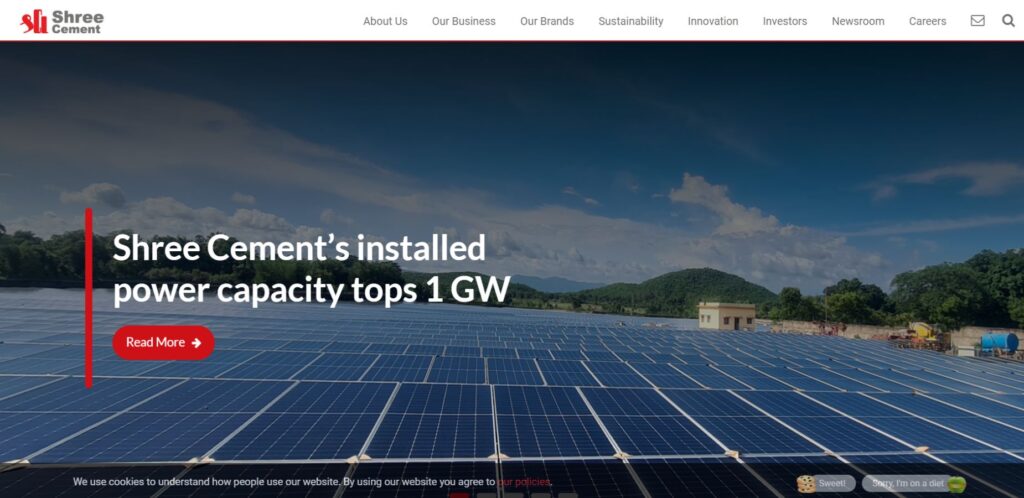
Shree Cement Limited, established in 1979, has become a leading cement producer in India and the industry standard for energy efficiency and environmental sustainability. Based in Kolkata with roots in Rajasthan, the company has long enjoyed a reputation for cost leadership, innovative plant operations, and commitment to environmentally friendly manufacturing practices.
Shree Cement is specifically known to have the smallest carbon footprint in the world cement industry and continues to be at the forefront in addressing India’s increasing housing and infrastructure requirements through sustainable and high-quality cement offerings.
Production Capacity:
- Current installed capacity: Approximately 53.4 million tonnes per annum (MTPA)
Recent additions:
- 3 MTPA grinding unit in Purulia, West Bengal
- 3.5 MTPA integrated plant at Nawalgarh, Rajasthan
Expansion plan:
- Investing ₹7,000 crore to add 12 MTPA in Rajasthan, Uttar Pradesh, and Karnataka by 2025
- Long-term target of reaching 80 MTPA by 2028
Key Plants/Locations:
- Rajasthan: Beawar, Ras, Jobner, Khushkhera, Suratgarh – core manufacturing hub
- Uttar Pradesh & Uttarakhand: Units in Bulandshahr, Panipat, Laksar
- Chhattisgarh, Jharkhand, Bihar: Plants in Raipur, Seraikela, Aurangabad
- West Bengal & Karnataka: Purulia (grinding unit), Nawalgarh (integrated unit with northern market focus)
Sustainability Initiatives:
- Energy efficiency & green power:
- Holds the record for lowest energy consumption per tonne of cement in India
- Operates 126 MW of Waste Heat Recovery Systems (WHRS) – among the largest globally
- Around 39% of total power from renewable sources (WHRS, solar, wind)
- Carbon reduction & climate goals:
- Specific CO₂ emissions reduced by over 41% since 1990
- Recognized by Science-Based Targets initiative (SBTi) for aligning with Paris climate goals
- Targeting further reductions through synthetic gypsum use, high fly ash content, and fuel substitution
- Circular economy practices:
- Extensive use of fly ash, slag, bed ash, and synthetic gypsum
- Zero-waste plants with practices like sewage sludge composting and boiler ash recycling
- Water & biodiversity:
- Rainwater harvesting and recycling implemented at all major plants
- Ongoing plantation drives with 90,000+ saplings planted annually
Website: www.shreecement.com
6. Nuvoco Vistas Corp Ltd
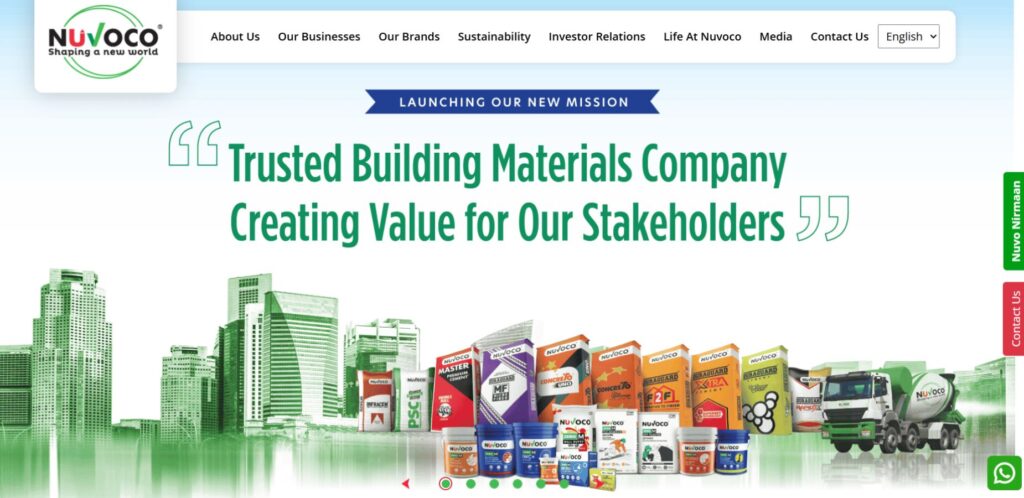
Nuvoco Vistas Corp Ltd, a subsidiary of the Nirma Group, is India’s fastest-growing building materials and cement company. As India’s fifth-largest cement player in terms of capacity, Nuvoco has a strong presence in Eastern and Northern India.
With a diversified business in cement, ready-mix concrete (RMC), and contemporary construction solutions, the company stands out with its innovation, customer-centricity, and sustainable practices. Nuvoco’s growth journey is driven by ongoing expansion, operational efficiency, and a focus on its environmental vision under the “Protect Our Planet” (POP) initiative.
Production Capacity:
- Current installed capacity: Approximately 25 million tonnes per annum (MTPA)
- Recent developments:
- Commissioned a 1.2 MTPA grinding unit in Haryana to strengthen its northern presence
- Ongoing debottlenecking projects at Risda and Nimbol plants to increase clinker production
- Future expansion: Acquisition of Vadraj Cement (3.5 MTPA clinker + 3.5 MTPA grinding) to raise total capacity to nearly 31 MTPA by FY 2027
Key Plants/Locations:
- Eastern & Northern India: Plants in Chhattisgarh, Odisha, Jharkhand, Bihar, West Bengal, and Haryana
- Key sites: Large integrated facilities at Risda and Nimbol
- Upcoming assets: Vadraj Cement units in Kutch (clinker) and Surat (grinding) to enhance western market reach
Sustainability Initiatives:
- Decarbonisation & emission reduction:
- Reduced specific CO₂ emissions to 457 kg per ton of cementitious material, among the lowest in the sector
- Lowered RMC emissions from 2.89 to 2.64 kg CO₂ per cubic metre
- Green energy & efficiency:
- 44.7 MW Waste Heat Recovery Systems (WHRS) operational across plants
- Solar energy capacity expanded from 1.5 MW to 5.3 MW
- Greener logistics: Over 175 CNG trucks including lightweight models for reduced emissions
- Alternative Fuels & Raw Materials (AFR):
- Increased thermal substitution rate (TSR) from 9% to 13%
- Chittor plant achieved 24%+ TSR, with enhanced feeding systems
- Circular economy & water conservation:
- Utilized 1.8 million tonnes of industrial waste
- Introduced Aqua Zero Debris Recycler in RMC operations, reducing water usage by up to 40%
- Raised alternative raw material (ARM) usage to 33.9%
- Biodiversity & community development:
- Planted over 115,000 native trees, creating a projected carbon sink of 1.1 million tonnes CO₂
- Recognized for sustainable mining and awarded for environmental best practices at several plants
Website: www.nuvoco.com
7. Ramco Cements Limited
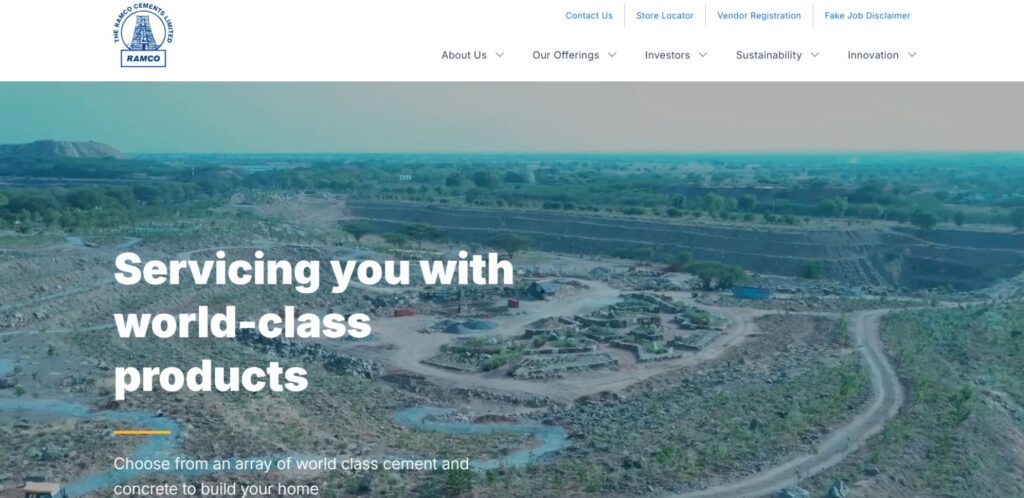
The Chennai-based Ramco Cements Limited is a top cement company known for its commitment to green energy, technologically advanced operations, and strong regional presence in South and East India. With an optimum combination of integrated plants and grinding units, Ramco has established itself as the benchmark for operational excellence, environmental care, and people-focused growth.
The strategic growth of the company, especially in the Odisha and Andhra Pradesh markets, emphasizes its resolve to drive India’s infrastructure growth while reducing its carbon output.
Production Capacity:
- Integrated plants: Five major facilities, including Virudhunagar (RN Nagar), Ariyalur, Alathiyur, Jayanthipuram, and the newer Kalavatala
- Grinding units: Six modern units in Tamil Nadu, West Bengal, Andhra Pradesh, Odisha, and Karnataka
- Total cement capacity: Estimated around 26 MTPA by FY 2026, alongside 19 MTPA clinker capacity
- Recent upgrades: Odisha’s grinding plant at Haridaspur increased to 1.8 MTPA
- Kalavatala integrated plant doubled clinker and cement output, enhanced by efficient debottlenecking
Key Plants/Locations:
- Ramasamy Raja Nagar (Virudhunagar, TN): 3 MTPA integrated plant, pioneering dry kiln processing in southern India
- Ariyalur & Alathiyur (TN): Combined ~6.5 MTPA capacity, advanced milling and automation systems
- Jayanthipuram (Krishna, AP): 3.65 MTPA integrated unit with modern ambient air monitoring
- Kalavatala (Kurnool, AP): Greenfield plant with ~2.4 MTPA capacity, backed by captive power and railway siding
- Grinding units:
- Odisha (Haridaspur): 1.8 MTPA
- West Bengal (Kolaghat): 2 MTPA
- Tamil Nadu (Valapady): 2 MTPA
- Andhra Pradesh (Vizag): 2 MTPA
- Karnataka (Mathodu): 0.29 MTPA
Sustainability Initiatives:
- Green energy dominance:
- 71% of clinker power is sourced from green energy (WHRS + wind)
- 39 MW WHRS operational at Jayanthipuram; Phase II expanding capacity
- Kalavatala set up with 12.15 MW WHRS, plus an 18 MW captive thermal plant
- Energy and emission optimization:
- Efficient use of waste heat to cut grid dependency and power costs
- Recognized for clean, dust-free manufacturing environments
- Community and environment stewardship:
- Restores water bodies, protects local biodiversity, and builds rural infrastructure
- Provides healthcare camps, educational efforts, and disaster relief in plant regions
- Awarded for sustainable practices and employee-driven CSR initiatives
Website: www.ramcocements.in
8. JK Cement Limited
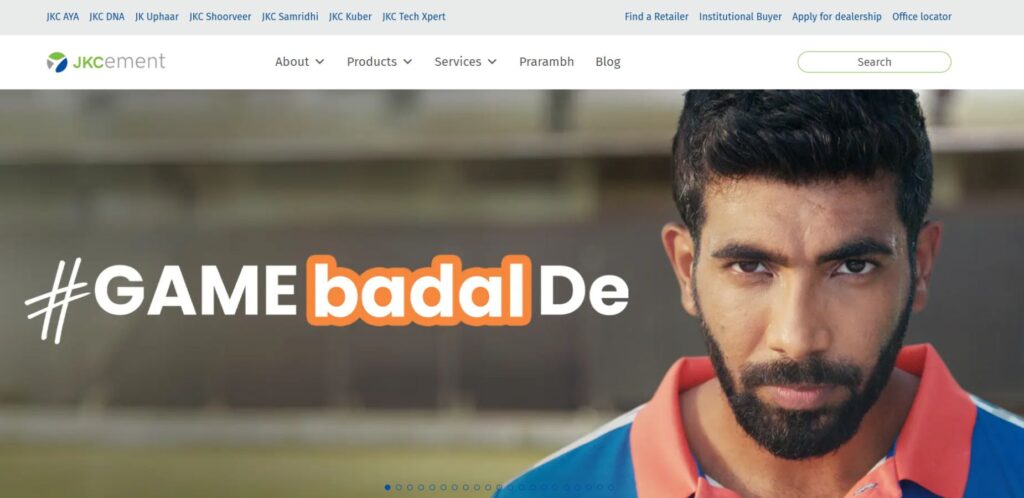
JK Cement Limited is India’s leading cement company, renowned for its strengths in both grey and white cement manufacture. Founded in 1975, the company has established a robust national and global presence through relentless innovation, operational excellence, and sustainable growth.
Having an expanding production capacity, cutting-edge manufacturing facilities, and decarbonization focus, JK Cement is a vision-oriented business playing its part actively in India’s infrastructure growth and global cement leadership.
Production Capacity:
- Grey cement capacity: Around 24–25 million tonnes per annum (MTPA)
- White cement & wall putty: Approximately 3.05 MTPA
- Expansion efforts:
- New clinker line in Panna, Madhya Pradesh has doubled capacity to 6.6 MTPA
- On track to double total production capacity by 2030 through greenfield and brownfield projects
Key Plants/Locations:
- Rajasthan: Major plants in Nimbahera, Mangrol, and Gotan
- Madhya Pradesh: New capacity added at Panna
- Uttar Pradesh & Karnataka: Significant grey cement operations
- White cement division: Strong international presence, exporting to over 36 countries
Sustainability Initiatives:
- Carbon reduction goals:
- Reduced specific CO₂ emissions from 680 kg to 563 kg/ton of cementitious material since FY2020
- Committed to Science-Based Targets and part of the Race to Zero initiative aiming for net-zero by 2050
- Green energy integration:
- Increased green energy usage from 19% to over 43%, targeting 75% by 2030
- Investments in wind-solar hybrid power projects to further lower fossil dependency
- Alternative fuels and raw materials:
- Current Thermal Substitution Rate (TSR) at 11%, with a target of 35% by 2030
- Significant use of fly ash, slag, and other substitutes to reduce the clinker factor
- Energy efficiency:
- Reduced electrical energy use to 63 kWh/ton, supported by WHRS, modern compressors, and digital automation
- Water and biodiversity:
- Water positivity improved to 4.6x, aiming for 5x by 2030
- Established a 50-hectare biodiversity park and planted over 1.1 million trees
- Circular economy efforts:
- Utilizes around 1.8 million tonnes of industrial waste annually
- Certified with GreenCo Platinum and Gold ratings for sustainable and zero-landfill practices
Website: www.jkcement.com
9. Dalmia Cement (Bharat) Ltd
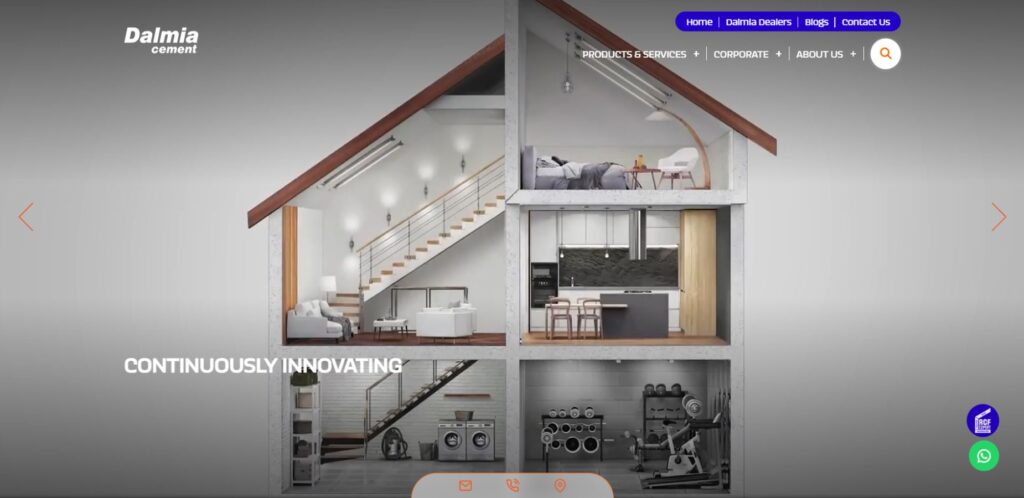
Dalmia Cement (Bharat) Ltd, a Dalmia Bharat Group flagship company, is among India’s most trusted and sustainability-focused cement producers. The group has its history dating back to 1939 and has evolved into the fourth-largest cement player in the nation, with operations spread across strategic markets with an aggressive focus on innovation, climate stewardship, and operational brilliance.
Renowned for its global standards of carbon efficiency, Dalmia Cement is a pioneer in the evolution to green cement, marrying scale, performance, and purpose to create a greener future for India’s infrastructure.
Production Capacity:
- Total installed capacity: Around 37 MTPA, across 14 units in 10 states
- Blended cement focus: 80% of its product range consists of lower-carbon, blended cements
- Portland Slag Cement leadership: India’s largest manufacturer, supporting eco-friendly infrastructure projects
Key Plants/Locations:
- Integrated and grinding units across Tamil Nadu, Odisha, Chhattisgarh, Bihar, West Bengal, Maharashtra, Karnataka, Gujarat, Uttar Pradesh and Rajasthan
- Notable sites include Rohtas (Bihar, with floating solar), multiple Eastern India facilities leading in low-carbon cement production
Sustainability Initiatives:
- Renewable energy drive:
- Installed 113 MW solar capacity and 72 MW waste heat recovery systems (WHRS)
- As a member of RE100, targets sourcing 100% of electricity from renewables by 2030
- Carbon negative ambition:
- First cement company globally to pledge carbon-negative operations by 2040
- Achieved 467 kg CO₂/tonne, significantly lower than global averages
- Ranked #1 globally by CDP for lowest carbon footprint and climate-readiness
- Alternative fuels & circularity:
- Uses ~18% municipal solid and industrial waste in kiln fuel
- Approximately 40% of raw materials are from waste/by-products
- Plans to achieve 100% blended cement through ₹6,000+ crore investment
- Energy efficiency & water management:
- Energy productivity up by 57% since FY2011
- Move toward zero-liquid discharge and water positivity (currently 5× consumption)
- Saved ~17.6 million tonnes of CO₂ over the last five years through efficiency and renewables
- Sustainable mining practices:
- Low-impact mining with no secondary blasting, biodiesel-powered equipment
- Digital mine monitoring, afforestation in mined-out pits, rainwater harvesting
- Environmental & governance excellence:
- ISO 14001, ISO 50001 certified; first in sector to align with EP100, RE100 & EV100 campaigns
- Active CSR across 11+ states, with ISO 26000-aligned practices supporting rural communities and education
Website: www.dalmiacement.com
10. Anjani Portland Cement Limited
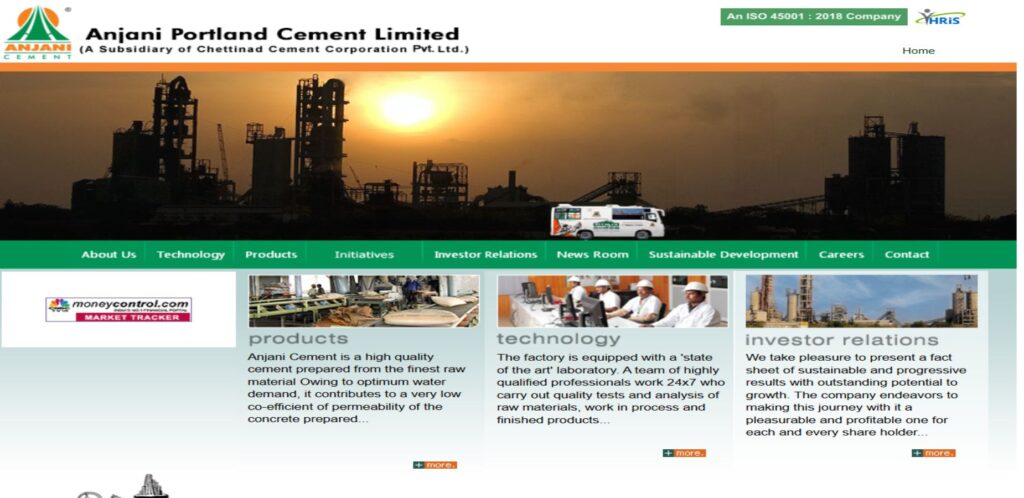
Anjani Portland Cement Limited, which is a part of the Chettinad Group, is a well-known regional cement manufacturer in South India that marries tradition and modernity.
Having begun operations in 1999 with a humble capacity, the company has grown consistently to emerge as a reliable name in Andhra Pradesh, Telangana, Tamil Nadu, Odisha, Karnataka, Maharashtra, Kerala, and Goa. Recognized for its focus on quality, innovation, and social involvement, Anjani Cement functions with state-of-the-art technology while being very strong environmentally as well as socially.
Production Capacity:
- Total installed capacity: Approximately 1.16 million tonnes per annum (MTPA)
- Line I: 0.4 MTPA, commissioned in 1999
- Line II: 0.76 MTPA, added in 2010
- Capacity utilization: Averaged around 73%, with strong demand-driven operations and steady output
Key Plants/Locations:
- Primary integrated plant: Located in Nalgonda district, Telangana
- Equipped with 5-stage preheater and precalciner kilns for both production lines
- Strategic logistical reach across Andhra Pradesh, Telangana, Tamil Nadu, Odisha, Karnataka, Maharashtra, Kerala, and Goa
Sustainability Initiatives:
- Pollution control & certifications:
- Uses advanced Reverse Air Bag House (RABH) systems for effective dust collection
- Certified with ISO 9001, ISO 14001, and OHSAS 18001, reflecting best practices in quality, environment, and safety
- Energy efficiency:
- Automated control through Siemens PCS7 system for efficient milling and kiln operations
- Ongoing efforts in kiln debottlenecking, alternative fuels, and process optimization to reduce energy consumption
- Water conservation & greenery:
- Active rainwater harvesting and green zone development at plant sites
- Plantation drives to enhance ecological balance in surrounding areas
- CSR & community engagement:
- Operates Smt. Sita Memorial School to promote education near its plant
- Community development projects include drinking water supply, healthcare camps, road construction, and borewell installations in nearby villages
Website: www.anjanicement.com
You may also read this: FMCG Companies in India
Conclusion
India’s cement sector is a key driver of the nation’s infrastructure and economic development. As one of the world’s highest capacities in production, it continues to fuel urban expansion, rural growth, and industrial development’s expanding needs. These companies not only expanded operations but also played a significant role in nation-building—providing quality materials for homes, highways, ports, and power plants, among others. Their focus on performance, efficiency, and access has made them important facilitators of India’s change.
With the industry adopting cleaner technologies, alternate fuels, and more intelligent manufacturing techniques, it is on the cusp of a new era of responsible expansion. Beyond volume, attention is shifting to value-led, sustainable growth, creating opportunity for a more robust and environmentally conscious future for the construction sector.
FAQs
1. What is the best cement brand for building houses?
]Popular brands such as UltraTech, ACC, Ambuja, JK Cement, and Shree Cement are common for house construction. It really depends upon local weather, structural requirements, and whether you need OPC (Ordinary Portland Cement) or PPC (Portland Pozzolana Cement).
2. What are the various types of cement used in India?
Common ones are:
- OPC (Ordinary Portland Cement)
- PPC (Portland Pozzolana Cement)
- PSC (Portland Slag Cement)
- White Cement
- Rapid Hardening Cement
Each is used to meet various construction requirements in terms of strength, setting time, and exposure to the environment.
3. Is Indian cement exported to other nations?
]Indian cement is being exported to nations in South Asia, Africa, and the Middle East. Coastal plants, particularly in Gujarat and Tamil Nadu, make a large contribution to export quantities by virtue of being close to ports.
4. Are Indian cement firms investing in green technologies?
Yes, several top companies are targeting carbon reduction, alternative raw material and fuel (AFR) use, waste heat recovery technologies, and sustainable cement types to address global sustainability standards
5. What are the considerations in selecting a cement brand?
Keep in mind factors like cement grade (33, 43, or 53), type (OPC, PPC, PSC), brand reputation, setting time, climate compatibility, cost, and availability in your locality. Always check ISI certification and manufacturing date for quality assurance.